Don't
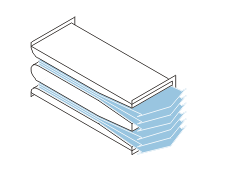
Don’t select a silencer with high attenuation and low percentage open area without checking the airflow generated noise level.
Do
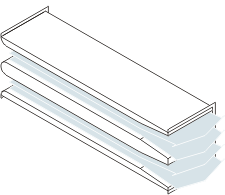
Do check silencer airflow generated noise levels when these conditions occur. If airflow generated noise is too high, try using a longer silencer with a larger open area to get the same attenuation at a lesser airflow generated noise, or acoustically treat the duct after the silencer.
As a general rule of thumb, a pressure drop of 30 Pa should limit the airflow generated noise of a silencer to an acceptable amount in normal office areas.