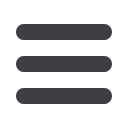

I
VIBRATION ISOLATORS
VIBRATION ISOLATORS
© FANTECH
2016
I-2
INTRODUCTION
VIBRATION ISOLATION
To isolate unwanted fan vibration, it was once sufficient to mount the offending
equipment on a piece of cork or felt. But today, with greater knowledge and higher
expected standards, this traditional solution is usually inadequate, both in large building
structures and in the general industrial environment.
In building construction, improved design allows lighter but inherently more flexible
structures to be used. At the same time, increasingly powerful equipment is needed
and may often be installed in upper level plantrooms. Fan vibration, therefore, can be a
major problem in such structures.
IMPORTANCE OF STATIC
DEFLECTION
Isolation of vibration is accomplished by supporting the equipment on resilient
mounting elements such as springs or rubber, which compress under the equipment’s
weight. The degree of isolation achieved is directly related to the amount of
compression (i.e. static deflection) of the mounting.
The greater the static deflection which can be achieved (without compressing to solid)
the better the resulting vibration isolation.
When determining the level of isolation efficiency which might be acceptable in any
situation, consideration must be given to the following:-
O
Fan type and operating weight.
O
Magnitude and nature of the vibrating forces.
O
Restrictions on fan motion.
O
Location of the fan in the building structure.
For example, an isolation efficiency of 80% is normally satisfactory for a 5kW machine
located in the basement but totally inadequate for a 100kW machine installed on a
flexible upper level floor, particularly when adjacent to valuable office or residential
accommodation. In this case an isolation efficiency close to 97% would be
recommended.
USING VIBRATION MOUNTINGS
Some simple guidelines for successful vibration control:
1. Mounting support points and load ratings should be selected so that the static
deflections of all mountings are as uniform as possible.
2. Unrestricted movement of resiliently mounted equipment is essential for effective
isolation.
a) Ensure that adequate clearance is maintained around the installed equipment,
particularly underneath it, to permit free movement - especially where high
deflection mountings are used.
b) All connections to resiliently supported equipment should themselves be
flexible. As well as restricting equipment motion, any fixed connection can
offer a direct path for transmission of vibration to the surrounding structure,
bypassing the isolation system.
3. Top-heavy machinery, especially when mounted on a narrow base, can become
unstable if mountings are located too close to each other beneath the equipment.
Such instability can be avoided by use of outrigger brackets which space the
mountings further apart and raise the mounting location points closer to the
vertical centre of gravity of the equipment.
4. A rigid base is essential for resiliently supported equipment to avoid misalignment
of drive components. Any flexibility in the machine base should be eliminated by
the addition of steel stiffeners or use of a concrete inertia base.
5. Ductwork and ancillary equipment should not impose dead loads on the resiliently
mounted equipment (such as attenuators). Where this is not possible, their weight
should be separately supported or allowed for when calculating the total weight.