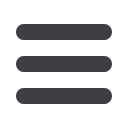

N-13
© FANTECH
2016
INSTALLATION, WIRING DIAGRAMS & FAN TROUBLE SHOOTING
5.0 ELECTRICAL (Cont.)
Problem
Possible Cause
Recommended Action
5.4 Electrical hum
Electronic speed-controllers can
generate an electrical hum.
If the electronic controller is not faulty
explore using a SSC single-phase
2-speed switch in its place. Alternatively,
use an auto-tranformer speed controller.
If a variable speed drive (VSD) is fitted
incorrectly it can cause a high level of
harmonics in the supply.
Check the installation conforms to the
VSD supplier's recommendations.
Phase imbalance on three-phase motor.
Check and correct the supply.
Motor is not designed for the electric
supply ie. wrong voltage or frequency.
Check the electrical supply matches the
motor nameplate.
Motor is overloaded and drawing greater
than the nameplate amps.
Check the correct motor is fitted. If
correct check the pitch-angle if an axial
fan or the belt-drive details if a belt-driven
fan. If these are correct contact the
supplier.
Motor has excessive clearance between
stator and rotor. In this situation the
motor will run slower than the normal
speed. ie. have excessive slip.
Check motor speed, if slow contact the
supplier.
5.5 Motor overheating or high
current draw.
Faulty instruments.
Ensure all instruments are accurate and
calibrated where necessary.
Incorrect power supply
Check the electrical supply matches the
motor nameplate.
Three-phase motor running with one
phase disconnected. This is called
single-phasing. When single-phasing, the
motor will draw uneven current on each
phase and will generally not start from
standstill.
If single-phasing, check if it is the power
supply or the motor windings. If a
winding has failed the motor may need to
be replaced. Fitting correct overloads or
phase protection will prevent this
problem.
Impeller has too much inertia for the
motor power and does not achieve full
speed.
Check the inertia of the load and reduce
as necessary. Alternatively, fit a larger
motor.
Excessive dirt on the motor cooling fins
so the heat is not able to dissipate.
Remove the dirt and dust on the motor
body and between the cooling fins.
Increase the maintenance frequency.
If the motor is out of the airstream either
the cooling fan is not fitted or the air inlet
to the motor cooling fan is obstructed.
Fit the motor cooling fan if not fitted and
remove any obstructions from the air inlet
to the motor.
Excessive stopping or starting - 10
starts/hour is generally acceptable.
Check the control system and reduce the
number of starts/hour as recommended.
A conventional three-phase motor is
connected in Delta when it should be in
Star, or vice-versa.
Check the motor nameplate and re-wire
correctly.
The fan impeller is jammed resulting in a
locked rotor situation. The motor will
draw 6-10 times the rated current in this
situation.
Check to ensure the impeller can rotate
freely.
A 2-speed motor, when switching from
high to low speed, can generate heat if
the supply is not switched off.
Switch off the power first and allow the
motor to run down before engaging low
speed.
Alternatively, use a time delay interlock.
Backward-curved centrifugal impellers
may be running in the wrong direction.
When running in the wrong direction they
will tend to overload the motor. Airflow
capacity will be down to approximately
30-40% of full flow.
Check and correct the direction of
rotation of the impeller if necessary.
FAN TROUBLE SHOOTING
N