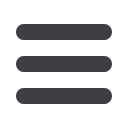

9
K-4
N
© FANTECH
2016
INSTALLATION, WIRING DIAGRAMS & FAN TROUBLE SHOOTING
INSTALLATION & MAINTENANCE
N
Belt-Driven Product
O
pulleys must be correctly aligned.
O
belts must be correctly aligned and tensioned.
O
tension must be checked 2-4 weeks after start-up.
Roof Ventilators
O
ensure that upstands are flat and true.
O
maximum angle of upstand or curb 30°
O
fix a sealing strip of neoprene to the top of the upstand to prevent air leakage.
O
fit an electrical compression gland to the roof cowl in an appropriate location
and pass the electric cable through as the roof cowl is fitted.
O
ensure the electric cable is not pinched prior to securing the cowl to the
upstand.
O
the roof cowl should be secured with roofing screws through the side skirt
midway through the skirt.
O
inlet ductwork should be free from obstructions.
O
avoid sharp bends at the inlet.
O
vertical discharge axial roof units: ensure the damper flap hinge points
down the slope of the roof.
LUBRICATION INSTRUCTIONS
Most Fantech products are fitted with sealed-for-life pre-lubricated bearings which do
not require maintenance for the life of the fan.
Should your fan be fitted with grease nipples, the following instructions should be
followed:-
RECOMMENDED
LUBRICATION INTERVALS
RECOMMENDED GREASES
Wherever possible the grease used should be identical to the original. When different
greases are mixed, even if they are both suitable for the conditions, incompatibility can
occur and result in rapid bearing failure.
In the absence of specific instructions supplied with the fan the following greases
should be used. STANDARD FANS Shell Alvania R3 or compatible lithium-based grease
suitable for 130°C continuous operation. SMOKE SPILL and high temp motors must use
the grease stated on the motor to maintain the Smoke Spill approval.
PROCEDURE
If the grease lines are not extended to the outside of the case the fan must be
electrically isolated for safety before work commences.
Clean the grease nipples with a clean cloth.
Introduce the new grease to all points while the fan is rotating until the old grease is
purged from the grease relief port normally located at the bottom of the bearing
housing. If it is required to manually rotate the impeller, the fan must be electrically
isolated to prevent accidental startup.
WARNING
INCOMPATIBLE GREASE, EXCESSIVE GREASE OR INCORRECT GREASE RELIEF
CAN CAUSE DAMAGE TO THE MOTOR.
Motor Frame 48 rev/sec 24 rev/sec 16 rev/sec 12 rev/sec
160
4000
8000
12000
20000
180-200
3000
7000
12000
16000
225-250
2000
6000
10000
13000
280
1000
5000
8000
13000
315
1000
3500
8000
10000
Maximum interval 12 months.
These times are a guide only and will depend on the motor manufacturer and actual running conditions.
Working Hours